開放機器目視検査
目視検査のDXにより、プラントの現場で開放機器の目視検査にあたる検査員が、タブレット端末で検査データを入力してクラウドサーバに送信します。その検査記録のデータからリアルタイムで報告書を作成することで、検査結果をスピーディーに提供します。日々の検査記録作成時間の大幅な短縮と残業時間の低減に寄与します。
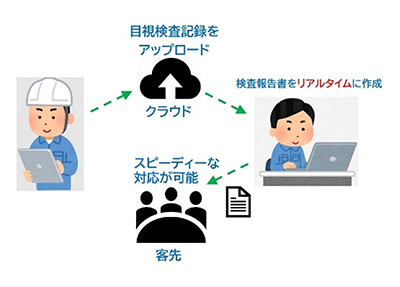
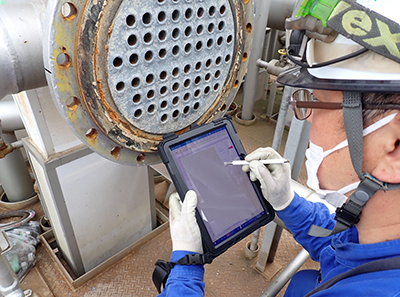
NON-DESTRUCTIVE INSPECTION
非破壊検査(NDI:Non-Destructive Inspection/ NDT:Non-DestructiveTesting)は、被検査物を物理的に破壊することなく、材料内部の欠陥や表面の微小なきず(割れや空洞)を検出する検査方法です。材料外部から材料内部へ放射線や超音波などを入射させて内部きずを検出、または材料表面へ電流や磁束を流して表面きずを検出する方法に大別されます。
当社は、建築物やプラントのドクターとして培ってきた技術と、DXによって進化させた独自の技術により、他に類を見ない非破壊検査サービスで、的確なデータを提供しています。
石油化学・精製プラントのSDM工事(定期修理工事)における目視検査で、野帳のデジタル化を実現。「検査員の残業時間低減・適正チーム数の配置・迅速な速報提出」を目指し、課題を解決する付加価値の高い技術とサービスを提供します。
目視検査のDXにより、プラントの現場で開放機器の目視検査にあたる検査員が、タブレット端末で検査データを入力してクラウドサーバに送信します。その検査記録のデータからリアルタイムで報告書を作成することで、検査結果をスピーディーに提供します。日々の検査記録作成時間の大幅な短縮と残業時間の低減に寄与します。
大型構造物の点検にドローンを活用することにより、点検作業の安全性や効率の向上、コスト削減を実現します。ドローンに搭載したカメラによる目視検査のほか、UT(超音波検査)ドローンを使った検査にも対応します。
非破壊検査員がドローンや超音波検査に対応するUTドローンなど、各種カスタマイズしたドローンを使った検査サービスを提供します。多様な検査ニーズに応えると同時に、検査における付帯費用の削減に寄与します。
多様な検査の条件や要求に対応すべく、スケールチェッカー・渦流アレイ・蛍光X線・ライブビデオX線・熱交チューブ極値解析・交流磁気などの特殊検査技術を用いた非破壊検査サービスを提供しています。
配管の目詰まりやスケールの堆積、赤錆の発生などプラント機器の現状を把握することは、故障予知や保全計画、そして運転状態の改善において必要不可欠です。当社独自開発の特殊非破壊検査装置「スケールチェッカー」は、微量な放射性同位元素(法規制外)を用い、配管の内部に付着した異物を測定・可見化することができます。
また、下記のような条件下においても内部の異物の測定や可視化による菅内の詰まり診断が可能です。
特殊な非破壊検査技術である渦流アレイは、複数のコイル(コイル数:32個・コイル径3mm)を用いることで、検査する欠陥範囲に対しプローブ長全体において高い検出能が維持できます。また、検査結果はわかりやすくカラー画像で表示して記録します。
渦電流アレイ検査には下記のような利点があります。
非破壊で金属材料の成分を判別することができ、下記のような特徴や仕様を持ちます。
熱交換器にて設備の信頼性を維持し安全運転を図るために、熱交換器チューブの抜管検査を行います。このシステムでは、肉厚測定システムと極値解析システムを組み合わせ、測定結果から熱交換器チューブ全体の余寿命を推定します。
特殊な非破壊技術であるMDKセンサーは、コイルで発生させた交流磁束が、試験体を透過して再びセンサーに戻ります。そのため、渦電流試験法で見られるような磁束の減衰がなく、試験体の外部や内部の情報を明らかにすることができます。
探傷事例として以下が挙げられらます。
FRP製のタンクなどは紫外線や内容物の腐食性により劣化が進行します。「フェイズドアレイ*3」によるUT診断(超音波診断)で劣化の把握が可能です。また、航空機や自動車の部品に使用されるCFRP製品の内部欠陥や層間剥離検査も行います。
プラントなどで使われるFRP(Fiber Reinforced Plastics:繊維強化プラスチック)、航空機や自動車などの部品に使われるCFRP(Carbon Fiber Reinforced Plastics:炭素繊維強化プラスチック)に対し、「フェイズドアレイ*3」によるUT診断(超音波診断)で、定量的な劣化や欠陥、層間乖離などの詳細検査を実施します。
*3 フェイズドアレイとは、現在使用されている超音波探傷検査技術の発展型といわれており、1つのプローブ(探触子)に複数個の振動子(アレイ)を備えている。この複数個のアレイを電気特性により制御して、角度・焦点距離・焦点ポイントを設定し、超音波ビームを作成。それにより、プローブを動かすことなく走査するビームの角度をすばやく変更し、優れた検出能力で欠陥を探傷できる技術。
当社独自の内面超音波探傷システム IRISを使った水浸UT検査(超音波検査)です。プラント設備などの熱交換器の伝熱管に水浸UT治具を挿入し、プローブ先端のミラーが水圧により360°回転しながら、超音波を伝搬させて全面検査(肉厚測定)を行います。
当社独自の非破壊検査技術である、内面超音波探傷システム IRIS(Internal Rotary Inspection System)を活用した水浸UT検査は、下記のような特徴を持ちます。
海外の産業プラントに向けて非破壊検査のサービスを提供しています。日本で培った検査技術で、グローバルな課題解決に貢献することを目指し、海外での事業に取り組んでいます。
インドネシアでは、1990年代に整備された製油所や化学プラントなど、多くの産業インフラが大規模メンテナンスの時期に到達しています。石油・ガス事業が現地の主要な輸出産業であるため、関連するプラントの維持管理や安全性の確保が求められています。
当社は、2016年からインドネシアの国営総合検査企業であるスコフィンド社(PT SUCOFINDO)と連携し、大手化学プラント向け非破壊検査業務(目視検査・配管スケールチェッカー・ボイラースケール測定・IRISなど)を行っています。また、2021年7月から毎年インドネシアアサヒマスケミカル社よりプラント定期修理における、開放機器目視業務及び渦流探傷検査、IRIS検査を受注しています。
お問い合わせ・サポート